
HOT
SALE
HOT
SALE
BEST
PLAN
BEST
PLAN
Frequently asked questions.
If you have a question that you can’t find the answer, please contact us!
How Do Different Raw Materials Affect Roller Die Lifespan?
There are several factors influencing the lifespan of roller shells of dry roller press granulator, including the type of raw materials during the extrusion granulation process. Moreover, roller molds are essential components, directly impacting the efficiency and longevity of the entire extruder granulation equipment. Here is an analysis of common raw materials and their impact on roller die longevity.

≤1500 Tons of Common NPK Powder Dry Granulation
In fact, if you use common NPK materials or certain mineral powders, it won’t cause more wear and tear on the rollers. Typically, under standard conditions, double roller fertilizer granulator can last up to 1500 tons of NPK granular fertilizer production. For example, urea, ammonium sulfate, ammonium chloride, calcium carbonate, limestone, zeolite, bentonite and other similar powder or lumps. Moreover, when extruding NPK fertilizer powder directly for granulation, you needn’t to add other auxiliary materials. However, if you make compound fertilizer granules from finer mineral powder, the extrusion pressure between the two rollers alone is not enough forming. Also, you can add 20% water appropriately for better granulation effect.
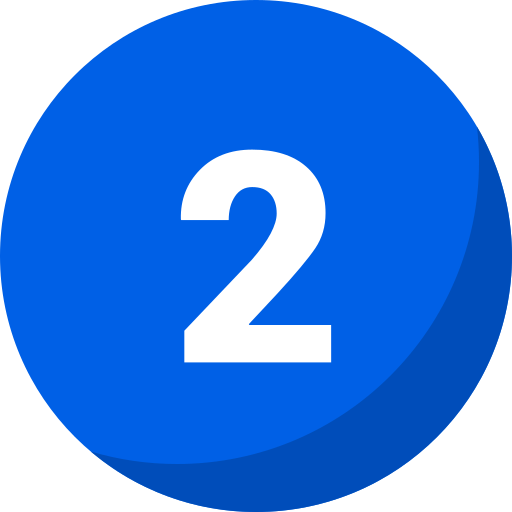
≤800 Tons of Corrosive Materials Roller Press Granulating
In general, some compound fertilizer materials are slightly acidic. When the rollers press these materials, the temperature will rise up. Therefore, through certain physical and chemical reactions, these raw materials can corrode the roll coating and ball socket shape over a long period of time. Honestly, this extruder pelletizer can produce approximately 800 tons of fertilizer granules from corrosive substance. For instance, you can use ammonium chloride, potassium nitrate, calcium chloride, calcium nitrate, manganous sulfate, monoammonium phosphate, etc. to make fertilizer pellets. What’s more, regular cleaning and maintenance can extend the service life of the roll dies.
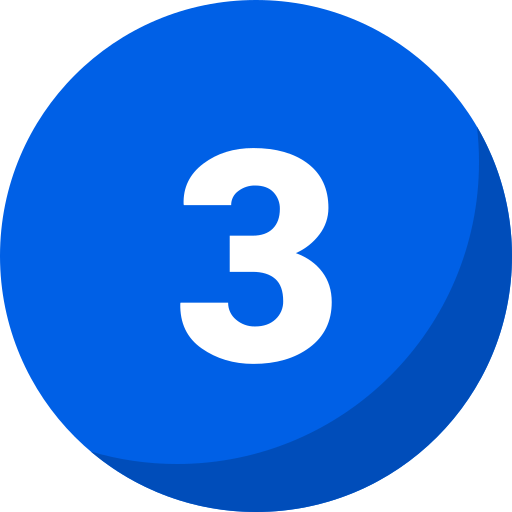
≤500 Tons of Organic Fertilizer Granule Compact Production
Indeed, organic fertilizer granulation raw materials include chicken manure, pig manure, kitchen waste, sawdust, bean dregs, biogas residues, mushroom residues and so on. At the beginning, you should handle these materials by compost machines for fermentation and decomposition. After organic fertilizer composting, these materials contain 30-35% moisture content. And you’d better age to reduce water for a few days before granulation. Because organic compost has high moisture and strong stickiness, it is easy to clog and damage the roll molds. As a result, double roller compaction pelletizer has a maximum lifespan of processing 500 tons of organic waste.
How to Extend The Service Life of Fertilizer Roller Granulator Machine?
Proper maintenance can significantly extend the service life of roller granulating machine. Firstly, regular cleaning is crucial. And you remove residues, especially when processing corrosive materials. Secondly, proper lubrication reduces friction and prevents the machine parts from wearing out prematurely. In addition, operators should avoid overloading the granulator, as excessive load can accelerate wear. Lastly, you should frequently inspect the roller skins for wear and tear. Then, you can replace worn-out parts promptly to prevent further damage.
Top 2 Metal Materials of Double Roller Sheets For Your Choice
The roller skin is a vital component of a double roller granulator, playing a pivotal role in the organic fertilizer or compound fertilizer granulating process. As you operate this machinery, good roller skin benefits the granule production efficiency and longevity of this equipment, and the quality of the final pellets. Thus, choosing the appropriare material to make the roller sheets is our duty for customers’ actual fertilizer granulation and cost-effectiveness.

Traditional Roller Skin Material of 20CrMoTi For Common Usage
To be honest, most of the roller press granulators on the market use 20CrMoTi as roller sheets. Indeed, it is a GB standard structural alloy steel with high performance. Also, it’s a carburizing steel, which is usually a low-carbon steel with a carbon content of 0.17%-0.24%. The composition of 20CrMoTi includes chromium, molybdenum, and titanium. After quenching, it contributes to the roller sheets’ hardness and wear resistance, meeting intense requirements of the dry granulation process. Additionally, 20CrMnTi steel has good weldability, small deformation, and good fatigue resistance. So we can easily carve all kinds of shapes for ball socket on the roller skins according to client’s needs. Its good hardness and toughness and can maintain roll dies non-deformation under high pressure over an extended period. Hence, we ensure that our extrusion granulators meet the rigorous demands of modern industrial applications by using 20GrMoTi.
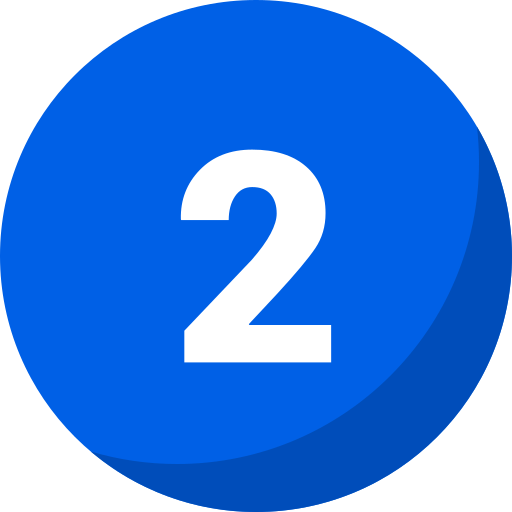
New Roller Skin Material of 4Cr13 For High-quality Granulation
In recently years, our company applies new material to manufacture double roller compact granulator, 4Cr13. Compared to the traditional alloy steel, 4Cr13 is martensitic stainless steel. What’s more, the special composition of 4Cr13 steel, including carbon, silicon and manganese content, contributes to its outstanding properties. Our factory quenches the roller dies made of 4Cr13 steel to get a harder surface. Compared to other steels, it is worth mentioning its excellent resistance to corrosion and polishing performance. So, the polishing property of this material also contribute to the beautiful and smooth surface of the roll pelletizer we produce. Therefore, this customization roll die of roller pressing granulator is ideal for handling corrosive raw materials like animal manure, etc. It prevents raw materials from sticking to the ball socket and corroding the equipment. Above all, using 4Cr13 steel as the roll dies’ material extends granulator’s service life in industrial granulation process.
What Is The Cost Difference Between Roller Sheet Materials 20CrMnTi And 4Cr13?
As a professional fertilizer equipment manufacturer, Yushunxin provides detailed information on the cost difference between roller sheet materials 20CrMnTi and 4Cr13. The market price for 20CrMnTi is approximately $1.2–$1.5 per kilogram, while 4Cr13 ranges from $2.0–$2.5 per kilogram. Typically, a roller granulator with a capacity of 1 ton per hour, is priced around $4000. Moreover, the roller molds made from 20CrMnTi would cost about $240-$300. In contrast, molds made from 4Cr13 would cost approximately $480-$600. Thus, customers can evaluate the material choice based on budget and performance needs.
The double roller extrusion granulator, also known as a dry granulation press or roller compactor, is a pivotal piece of equipment in the granulation process, which transforms fine powders into densified and compacted granules. The machine’s structural material is of paramount importance, as it needs to endure continuous operational stress and strain. For this reason, the main frame and components of the extrusion granulator are constructed from boiler steel, specifically the Q235 grade.
This material is renowned for its impressive strength and resilience, making it an excellent choice for heavy-duty machinery. Q235 boiler steel is characterized by its high tensile strength and yield point, ensuring that the machinery can withstand the substantial pressure exerted during the compaction process. Moreover, its resistance to deformation and cracking under stress guarantees a long service life for the granulator, ultimately leading to reduced maintenance requirements and operational downtime.
Thus, the utilization of Q235 boiler steel in the construction of the extrusion granulator not only ensures the robustness and longevity of the machinery but also underpinning the reliability and consistency of the granulation process.
FIRM
INTRO
FIRM
INTRO
TRUE
CASES
TRUE
CASES
Our Global Footprint
Yushunxin Machinery have been exported to 100+ countries and regions, for example, United States, UK, Spain, Australia, Russia, South Africa, India, Malaysia, Nigeria, Pakistan, Thailand, etc. , which are widely trusted by customers.
-
North America
Country: United States
Project: Bentonite Pellet Making Equipment
Capacity: 5 Million Tons Per Year -
South America
Country: Bolivia
Project: Phosphorus Rock Granulation Plan
Capacity: 2-4 Tons Per Hour -
Europe
Country: Norway
Project: Biochar Dry Granule Production Line
Capacity: 1.5 Tons Per HourCountry: Bosnia And Herzegovina
Project: Coal Dust Granulation Plan
Capacity: 500 kg-1 Tons Per Hour -
Africa
Country: Kenya
Project: Compound Fertilizer Production Line
Capacity: 1-2 Tons Per HourCountry: South Africa
Project: Compound Fertilizer Granulation Production Line
Capacity: 2 Tons Per Hour -
Asia
Country: Malaysia
Project: NPK Granule Fertilizer Manufacturing Line
Capacity: 220 Tons Per DayCountry: India
Project: Briquette Compaction Granulation Production Equipment
Capacity: 1 Tons Per HourCountry: Indonesia
Project: Organic Fertilizer Granular Production Line
Capacity: 1 Tons Per HourCountry: Thailand
Project: Rock Powder Granulation Production Proposal
Capacity: 2 Tons Per HourCountry: Pakistan
Project: NPK Fertilizer Dry Granulation Line
Capacity: 2 Tons Per Hour