Top 2 Metal Materials of Double Roller Sheets For Your Choice
The roller skin is a vital component of a double roller granulator, playing a pivotal role in the organic fertilizer or compound fertilizer granulating process. As you operate this machinery, good roller skin benefits the granule production efficiency and longevity of this equipment, and the quality of the final pellets. Thus, choosing the appropriare material to make the roller sheets is our duty for customers’ actual fertilizer granulation and cost-effectiveness.

Traditional Roller Skin Material of 20CrMoTi For Common Usage
To be honest, most of the roller press granulators on the market use 20CrMoTi as roller sheets. Indeed, it is a GB standard structural alloy steel with high performance. Also, it’s a carburizing steel, which is usually a low-carbon steel with a carbon content of 0.17%-0.24%. The composition of 20CrMoTi includes chromium, molybdenum, and titanium. After quenching, it contributes to the roller sheets’ hardness and wear resistance, meeting intense requirements of the dry granulation process. Additionally, 20CrMnTi steel has good weldability, small deformation, and good fatigue resistance. So we can easily carve all kinds of shapes for ball socket on the roller skins according to client’s needs. Its good hardness and toughness and can maintain roll dies non-deformation under high pressure over an extended period. Hence, we ensure that our extrusion granulators meet the rigorous demands of modern industrial applications by using 20GrMoTi.
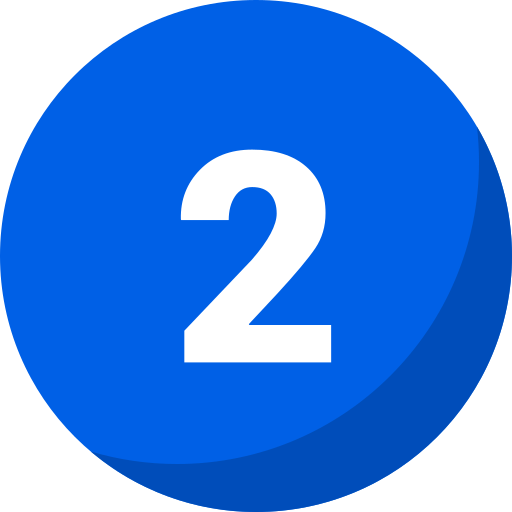
New Roller Skin Material of 4Cr13 For High-quality Granulation
In recently years, our company applies new material to manufacture double roller compact granulator, 4Cr13. Compared to the traditional alloy steel, 4Cr13 is martensitic stainless steel. What’s more, the special composition of 4Cr13 steel, including carbon, silicon and manganese content, contributes to its outstanding properties. Our factory quenches the roller dies made of 4Cr13 steel to get a harder surface. Compared to other steels, it is worth mentioning its excellent resistance to corrosion and polishing performance. So, the polishing property of this material also contribute to the beautiful and smooth surface of the roll pelletizer we produce. Therefore, this customization roll die of roller pressing granulator is ideal for handling corrosive raw materials like animal manure, etc. It prevents raw materials from sticking to the ball socket and corroding the equipment. Above all, using 4Cr13 steel as the roll dies’ material extends granulator’s service life in industrial granulation process.
What Is The Cost Difference Between Roller Sheet Materials 20CrMnTi And 4Cr13?
As a professional fertilizer equipment manufacturer, Yushunxin provides detailed information on the cost difference between roller sheet materials 20CrMnTi and 4Cr13. The market price for 20CrMnTi is approximately $1.2–$1.5 per kilogram, while 4Cr13 ranges from $2.0–$2.5 per kilogram. Typically, a roller granulator with a capacity of 1 ton per hour, is priced around $4000. Moreover, the roller molds made from 20CrMnTi would cost about $240-$300. In contrast, molds made from 4Cr13 would cost approximately $480-$600. Thus, customers can evaluate the material choice based on budget and performance needs.