
What are the distinct characteristics of 20CrMnTi and 4Cr13 in granulation?
Firstly, 20CrMnTi has high strength, good wear resistance, and excellent hardenability after carburizing and quenching. Thus, it makes it ideal for parts subjected to high pressure and wear, such as gears in pelletizing equipment. However, its machinability and weldability are relatively average, which may require more precise manufacturing processes. Conversely, 4Cr13 stands out for its high wear resistance and corrosion resistance after heat treatment, which is essential for environments where the equipment is exposed to corrosive materials during granulation. Also, it offers a superior surface finish after polishing, making it suitable for parts where aesthetic appearance is important. For clients focused on a smooth, durable finish in their pellet making machines, 4Cr13 provides a significant advantage.
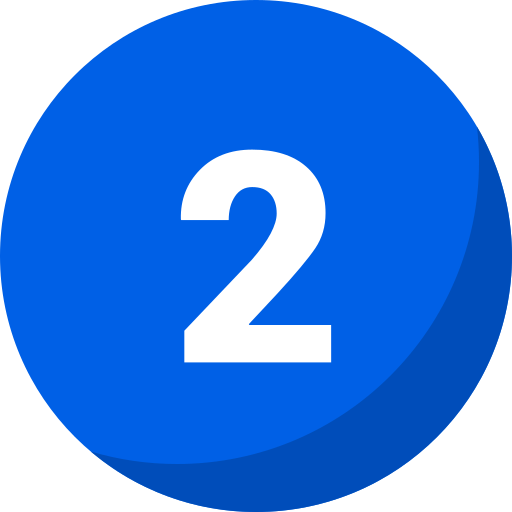
How do the physical and mechanical properties affect double roller extrusion granulators?
The physical properties of these two materials also differ significantly. 20CrMnTi has a density of 7.85 g/cm³, a melting point ranging from 1425°C to 1460°C, and a thermal conductivity of 46.6 W/m·K at 20°C. These properties make it stable under high temperatures, which is crucial for the high-pressure environment of dry granulation. In contrast, 4Cr13 has a slightly lower density of 7.75 g/cm³, a melting point of 1450°C to 1510°C, and a lower thermal conductivity of 24.9 W/m·K. This material is less thermally conductive but offers better resistance to thermal expansion with a lower thermal expansion coefficient of 10.2 µm/m·K compared to 11.8 µm/m·K for 20CrMnTi. Mechanically, 20CrMnTi boasts a tensile strength of 835–1080 MPa and a hardness of 55–62 HRC after heat treatment, which provides the necessary toughness and wear resistance for the granulation process. In contrast, 4Cr13, with a tensile strength of 735–980 MPa and a hardness of 48–54 HRC, offers slightly lower strength but compensates with superior wear and corrosion resistance, making it suitable for environments with abrasive or corrosive materials. Clients seeking high durability in a corrosive environment might prefer 4Cr13 for their pellet making machinery.
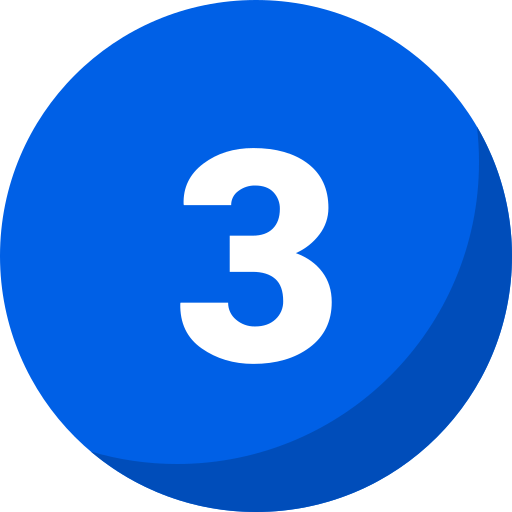
What chemical differences should you consider when selecting Material for your NPK granulation equipment?
Chemically, 20CrMnTi contains 0.17–0.24% carbon, 0.80–1.10% manganese, 1.00–1.30% chromium, and 0.04–0.10% titanium. The presence of titanium and chromium enhances its hardenability and wear resistance, making it suitable for heavily loaded parts in a granulating machine. In contrast, 4Cr13 has a higher carbon content of 0.36–0.45% and 12.00–14.00% chromium, which provides excellent corrosion resistance, an essential factor in processing certain fertilizers that might be corrosive. The high chromium content in 4Cr13 is particularly advantageous in preventing corrosion, making it ideal for applications where the machine is exposed to aggressive chemicals.